March 1, 2019
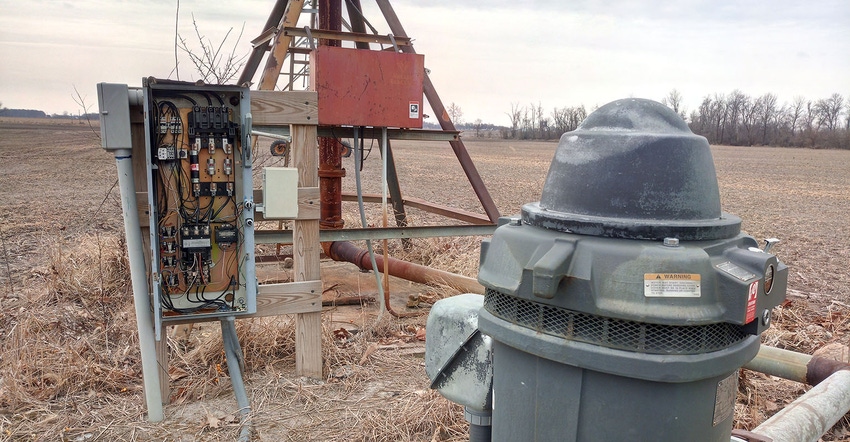
Anyone done much with VFDs? I’ve decided I will soon have my first experience. Variable Frequency Drives have many applications, but until now I have had no need to learn much about them. From my basic understanding, the magic that happens inside the drive changes the frequency of power supplied to a motor. A reduction in frequency causes a reduction in motor speed.
Common applications on the farms are for fans or pumps. You can even use a VFD in place of a phase converter, and be able to use 3-phase equipment where you only have access to single phase power. VFDs are supposed to be a real energy saver. If a motor only needs to run at 80%, then the VFD runs the motor at 80% and power consumption goes down. VFDs can be controlled by other devices such as pressure transducers or flow meters.
That is about the extent of my knowledge (or lack of) on VFDs.
Irrigation well pump
The application I plan on using a VFD for is the well pump for the new irrigation systems I have going in. Unfortunately, these are only 40-acre systems. As the End Gun comes on and shuts off, there can be a large swing in system pressure and volume because the pump has to be sized for maximum watering rate. An end gun adds wetted area beyond the pivot structure in the corners of fields. Often, they shoot 75-100 feet and consume around 60-120 gallons per minute. It is not uncommon for this to be 15% of the total water flow.
So, as spring slowly makes it way, I have been compiling parts from ebay and online stores. As soon as I receive the last batch of parts, I will start assembling and wiring them to make them ready to install at the farm. We are fairly comfortable doing most of our own electrical work, and since I’m the one that will end up serving the panel, I might as well learn now.
I don’t have an estimate of energy savings yet, but I did a traditional starter panel set up about 5 years ago on a very similar irrigation installation, so I will have a comparison. Initial cost looks to be 3 times more expensive than that panel which was made with used components. With a mixture of new and used parts, I should come in around $3,000 for a 50-hp 480-volt panel.
I’m hoping it’s a quick cost recovery. None the less, the system will be more accurate and apply water at more consistent rates.
The opinions of the author are not necessarily those of Farm Futures or Farm Progress.
About the Author(s)
You May Also Like