June 25, 2018
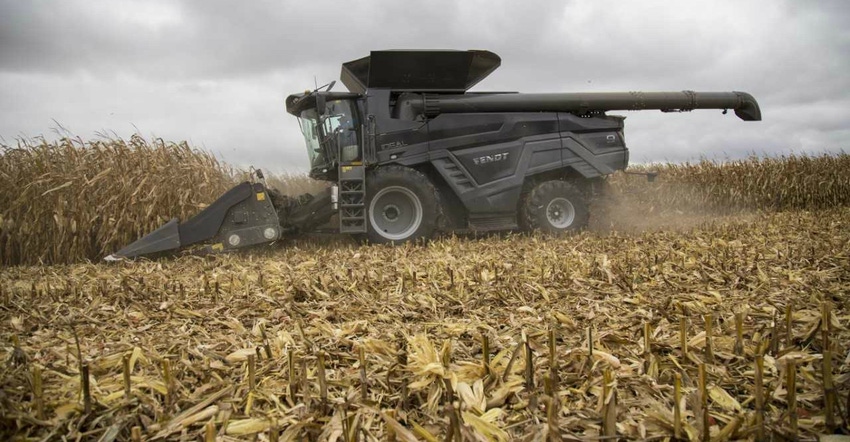
There's a black combine on the horizon, and it's heading for the North American market. Recently, ahead of a major farm show in Canada, Agco showed off the new Ideal Combine. The company claims it is the first "clean sheet" design for a combine in 30 years, and the new machine brings a lot of new tech along for harvest, as well as a new threshing system and a major uptime commitment. But why a new combine now?
"We had the opportunity as a global company to come together and say, 'How do we make a platform that will not only do what each region needs, and still be a global combine?'" said Caleb Schleder, Agco marketing manager for harvesting products, North America. "We didn't want to have seven to nine platforms across the globe."
Currently, Agco has one combine design in Europe, two key ones in North America and one in South America. The company is aiming toward a global platform. A single design, Schleder said, would let the company focus resources in support and engineering of a single platform. The result: the Ideal Combine. While it won't be replacing other combines in the line anytime soon, it does show the ability to be set up to harvest any crop where a combine is used around the world.
This is what engineers call a "clean sheet" design, which means engineers know the basic concepts they need to achieve, but they have no preconceived ideas of how to get there. The result is a totally new design for the threshing system from top to bottom.
Digging in on design
The new Ideal will be marketed as a Fendt machine and is an axial rotary combine. the two larger Class 8 and Class 9 machines use a dual rotor, while the Class 7 machine has a single rotor.
"They're called dual-helix rotors," Schleder said.
As a global combine, he said years of testing went into the new design. "We spent five years in the field doing major testing," he said. "We did truly specific testing in North America with canola in Canada, and we've been across the Midwest for different types of corn."
The aim was to run that machine in the extremes for any crop in a range of situations. "We wanted to go into high-moisture, high-yielding corn; low-moisture, high-yielding corn; high-moisture, low-yielding corn; and low-moisture, low-yielding corn," he said. "We call it ‘corner conditions,’ where we're working in the most extreme conditions for each crop."
The aim was to develop a combine that offered low grain loss and a clean grain sample in a range of conditions and for all major crops from canola to soybeans.
The Ideal Balance cleaning shoe is a full-width design that works even on hillsides to manage material flow. The system has two pans designed for even crop distribution.
The combine uses the Ideal Harvest system, which brings together an array of sensors that allows the producer to visualize grain moving through the machine.
Schleder said the system can provide operators the information they need for optimum setup. And for the operator that wants the combine to do the thinking and make setup changes on the go based on sensor information, the Ideal Harvest system can do that, too. The innovation is that those sensors are providing a lot of data to the operator through the in-cab monitor at all times.
The cab is based on the latest Gleaner S9 Vision Cab, which offers a 180-degree view and plenty of glass for visibility. The grain tank holds 485 bushels of grain, and the unloading auger boasts a 6-bushel-per-second unload speed.
"It's a very big grain tank. And when a lot of people look at these machines and think about capacity, they learn that grain handling is the governor on the process," Schleder said.
The key is keeping the combine moving, and a farmer's ability to move grain off the machine with support equipment. The larger grain tank and high-speed unloading auger help with that process.
The three models, Schleder said, are named according to class size — the Ideal 7, Ideal 8 and Ideal 9. Horsepower ranges from 450 to 650 depending on model size, and the Airsense system makes sure the engine runs at a constant temperature.
The company is running in-field demonstrations through dealers starting with the 2018 harvest. A limited number of machines will be in the market for the 2019 harvest. Learn more by visiting idealharvesting.com.
Agco did produce a video showing the new threshing system, we've added it below. Enjoy:
About the Author(s)
You May Also Like