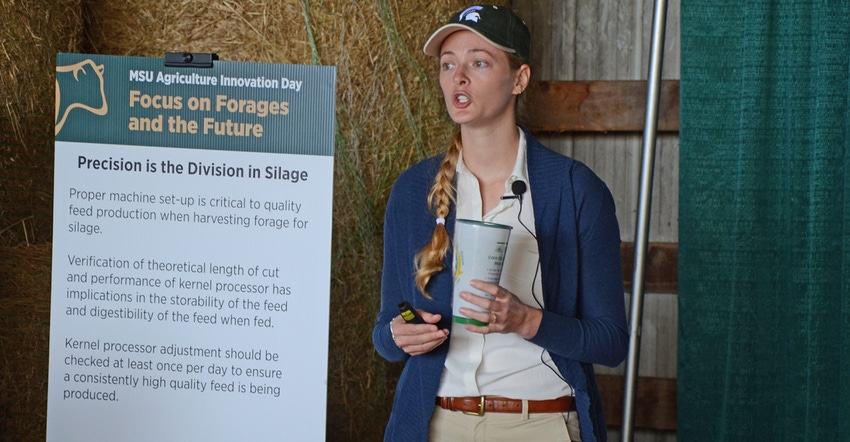
When asked how many participants at the Michigan State University Ag Innovation Day knew their KPS — Kernel Processing Score — only a few raised their hands.
Jessica Drewry of the University of Wisconsin-Madison said she hoped there would be more in the future, as she unveiled a new app the university developed for determining KPS.
Researchers at UW found that smaller corn kernel size can make starch utilization in dairy cows more efficient, which can lead to increases in milk production. Adjusting machinery settings — the cutterhead and kernel processer roll clearance on the combine — can ensure that quality.
Drewry said producers have different goals when crushing and shearing particles, because there is a trade-off with finer forages requiring more fuel and causing more wear and tear on machinery.
UW recommends the gap between the kernel processor rollers be set at 1 to 3 mm (about the thickness of a dime), and the theoretical cut length set to 19 mm. Knowing your KPS during harvest allows for adjustments, she said.
Lab samples are dried and passed through progressive sieves to determine the percentage that can pass through each screen. Samples are then scored:
• Optimally processed — 70% of kernels pass through the screen
• Adequately processed — 50% to 69% of kernels pass through the screen
• Inadequately processed — less than 50% of kernels pass through the screen
“Traditionally, farmers send a sample off to the lab, which will provide accurate and reliable date, but it’s too little, too late,” she said. “You can send that sample off and maybe a day, or a week later, you get your results back. By that time, you’re done with harvest, and there’s no way to correct any shortcomings you had. That may lead to having to add supplements to your feed.”
One method of on-the-spot checking is a silage cup, about the size of a large McDonald’s beverage cup. “You want to grab a cupful and sift through it looking for unbroken kernels,” she said. “You want only one per cup, no more.”
Another tool is the Penn State Particle Separator, which uses stacked trays. A sample is placed in the top tray, and then together the box stack is shaken consistently for 40 seconds, similar to the lab method. However, it is sensitive to the rate of shaking and the moisture content of the sample. “The caveat is it is dependent on the person who does it and how it’s shaken,” Drewry said. “Two people may come up with two different results. However, it’s still valuable to have that data point in the field to make corrections.”
Again, optimal processing means finding no more than one whole kernel for optimal processing. The same is true for the water separation method, which includes:
• filling a dishpan (or similarly sized container) about three-quarters full with water
• placing the representative forage sample in the container
• gently stirring the material, for about a minute, to separate the stover from the kernel. (The stover will float while the kernel will sink.)
• skimming the stover from the surface and slowly pouring the water from the dishpan to ensure the kernels remain in the dishpan
To take this method to another level, UW has created an image-processing software for either a smartphone or tablet to determine the level of kernel processing. Once the kernel pieces are separated from the stover and dried with paper towel, they should be put on a dark background, Drewry advised. “A black piece of construction paper works great,” she said. “Then use any U.S. coin as size reference, place it on the paper with the kernel pieces and take an image.”
The software in the newly developed mobile application SilageSNAP filters the photo to make the kernels stand out, detects the edge of each kernel, finds the coin at the center of the photo to serve as a scale, and determines the size of each kernel in the image. Drewry says this method results in recordable data that can be used to gain insight into trends between fields and to potentially spot kernel processor maintenance and wear issues.
“You really get a better sense of size distribution of those particles,” she says. “This can be used with silage, if you want to check before feeding, but it is more difficult than with freshly chopped silage. You will have stover left over with the kernels that will need to be picked out by hand.”
The image processing application will display the KPS and a histogram of particle size. A worksheet can be used to analyze the results to determine the particle size distribution. If 70% of the kernels are smaller than 0.187 inch in diameter, the kernel processing rolls are set to an appropriate gap. If not, they should be adjusted.
While harvesting, Drewry suggested conducting the Penn State test, which costs about $300 to purchase, and using the SilageSNAP app to estimate KPS every morning and using the silage cup test throughout the day. “Send a sample off to lab at end of harvest,” she adds. “But if you’re looking for better, accurate, reliable and recordable data, these other methods help to make adjustments when it counts.”
Drewry estimated the SilageSNAP to cost no more than $3, which will allow for continued research. It is expected to be available this fall, and it will be on iTunes and Google Play stores and UW-Madison CALS.
For more detailed description and photo of the water separation method, visit Team Forage.
Precision is the division in silage
Follow these steps to high-quality feed:
• Proper machine setup is critical to quality feed production when harvesting forage for silage.
• Verification of theoretical length of cut and performance of kernel processor has implications in the storability of the feed and digestibility of the feed when fed. Kernel processor adjustment should be checked at least once per day to ensure a consistently high-quality feed is being produced.
• Using tools such as visual assessment, water separation and SilageSnap can provide actionable data during harvest and during feeding to adjust and optimize total mixed rations.
• Kernel processor setting is important for high-quality feed, but also impacts machine and harvester efficiency. The smaller the roller gap the more energy is required to harvest the crop. Optimizing the roll gap could increase harvest speed and efficiency while maintaining sufficient kernel processing. SilageSnap will help us do that.
About the Author(s)
You May Also Like