March 18, 2010
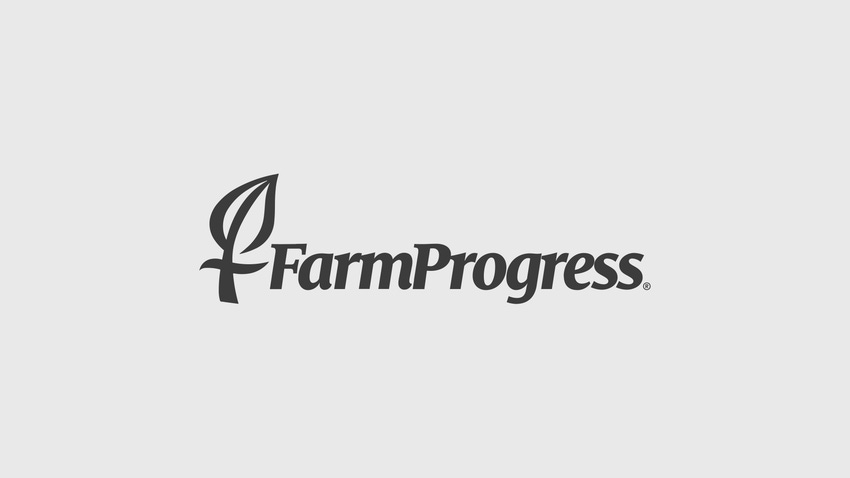
The salmonella threat in peanuts at the processing level last year pushed the U.S. industry to seek additional ways to strengthen food safety efforts across the supply chain — grower, sheller and manufacturer.
In a response to the food safety problem, organizations including the American Peanut Council, Birdsong Peanuts, and JLA USA conducted listening sessions with farmers in peanut-growing regions. Growers were asked to detail where food safety risks could exist at the grower level and to offer solutions to reduce the likelihood.
“Peanuts are food ingredients, so food quality is established at the farm,” said Darlene Cowart, director of food safety and quality, Birdsong Peanuts, Blakely, Ga.
Cowart headlined the grower meeting discussion and discussed food safety ideas during the 2010 Southern Seed Association annual meeting in Phoenix, Ariz. The grower think sessions included a risk assessment analysis based on the hazard analysis and critical control point system (HACCP).
Food safety is a top priority across U.S. agriculture from almonds in California to pecans in Texas to sweet potatoes in North Carolina. The U.S. spinach industry still struggles from lagging sales following an E. coli outbreak in California in fall 2006.
According to the Centers for Disease Control in Atlanta, Ga., about 76 million food-borne illnesses are reported annually. About 5,000 deaths occur and about 300,000 people are hospitalized. Some illnesses are never reported.
Cowart said growers are the first link in the peanut food safety chain. Peanuts are food ingredients, not just commodities, and peanut quality is first determined at the farm level. Good agricultural practices and the latest technology incorporated in a farm management program can result in high quality peanuts.
Good agricultural practices include documentation and employee training, ideal land selection and crop rotation, soil fertility, irrigation, animal exclusion and pest control, pesticide usage, and equipment maintenance and sanitation.
“If it’s not documented, it’s not done,” Cowart told the seedsmen. “Anything done at the farm level must be documented. You must be able to show people you did it.”
Specific documentation should include cropping history information, varieties and planting dates, crop management activities, pest reports from scouts and consultants, pesticide application records, fertilizer and soil amendment use, worker training information, and equipment records.
“Traceability proves what growers have done on the farm,” Cowart said. “Every grower needs to have their ducks in a row.”
Crop rotations every three to four years optimize peanut yields and quality. Employee training helps ensure worker safety around pesticides. Employees should understand how to properly operate, calibrate, maintain, and sanitize equipment.
Land selection is important as peanuts grow more efficiently in sandy, well-drained soils.
Cowart recommends farmers avoid planting fields containing excessive rocks, gravel, and other foreign material. Steer away from fields prone to excessive flooding from ponds and streams or runoff from livestock operations. Do not plant peanuts directly next to a livestock grazing operation, a potential source of E. coli and salmonella.
“Keep wildlife, including feral hogs, out of fields as much as possible,” Cowart said. “This may mean bordering your land with traps and reducing forestation to reduce a harboring area.”
Peanuts respond better to residual fertility from previous crops than from direct fertilization, according to Cowart. Peanuts are legumes that synthesize internal nitrogen, reducing the need for additional organic or inorganic nitrogen.
Cowart said farmers should make sure fertilizer does not contain heavy metal residues or excessive nutrient amounts, especially for the peanut export market.
Use of raw manure is not recommended in peanut production; composted manure is okay. She said stacked and aged manure is not equivalent to composted manure. If raw manure is used, apply it on the crop preceding peanuts.
A raw manure application in a peanut crop should be incorporated into the soil by March 1.
Raw manure piles should not be stored on or near peanut fields since water runoff can transport manure into fields. Composted manure should be prepared according to the National Organic Program.
Peanuts require 1 to 1.5 inches of water per week during the growing season. About 40 percent of the U.S. peanut crop is irrigated. About 85 percent of irrigated water is supplied by underground aquifers and wells.
Guidelines for irrigation include: inspect irrigation water sources; mix and load pesticides away from water sources to protect the water from chemical contamination; follow chemigation guidelines; and, preferably, do not use reclaimed water. (State guidelines for water treatment should be followed if reclaimed water is permitted by the state.)
Animal exclusion and pest control are critical issues in food safety. Cowart suggests growing peanuts away from large wildlife populations when possible. Remove trees and harborage areas around the field. Consider physical and chemical repellants, traps and barriers.
“Birds are major carriers of salmonella,” Cowart said. “Bird netting and bird nest removal may be necessary in shed areas.”
Other ideas include inspecting fields for pest activity and keeping trash and old equipment out of fields.
Cowart calls integrated pest management (IPM) the foundation for pest control in peanuts. A good IPM balance includes: crop rotation; biological, chemical, and cultural control practices; as well as crop forecast and disease prediction models.
When pesticide use is warranted, Cowart encourages labeled pesticides. Growers must be certified by local and state agencies to apply pesticides.
Regular equipment maintenance and sanitation is important.
“Carefully inspect all equipment for mechanical problems that could cause foreign material to end up in stock peanuts,” Cowart said.
“Also clean harvest equipment and trailers prior to harvest to remove previous peanut crop debris — a harborage area for bugs, rodents, insects, bird nests, and dirt.”
If wet washing equipment, allow adequate drying time since water is a major problem in microbial activity.
Another suggestion is to minimize loose-shelled kernels (LSK) in equipment.
“LSKs can be a high food-safety risk by rubbing against another item with bacteria,” Cowart said.
“Reducing LSK numbers reduce food safety risks.”
Food safety requires all segments of the industry to work toward the common goal of supplying the safest and most wholesome food product to consumers, Cowart said.
email: [email protected]
You May Also Like