April 13, 2010
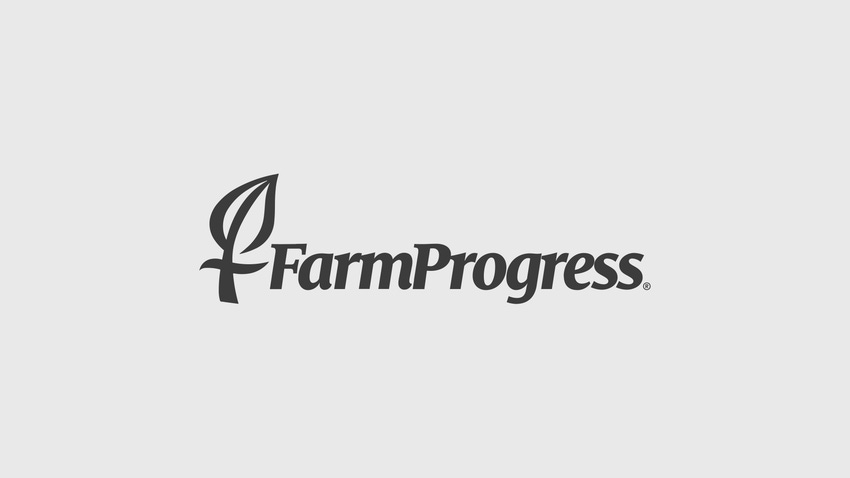
One of the most efficient energy saving strategies, but also one of the least used, is the proper use of a wet-bulb thermometer.
COMPUTERIZED controls outside the actual curing area make it easier to keep humidity and temperature at desired levels, says Sherrill Strickland.
Keeping the heat and humidity at the right level in a flue-curing barn is one of the biggest challenges in producing the crop. For most of the history of this tobacco type, the process has been more of an art form than science.
But equipment that allows for automation of part or all of the process is helping growers do a better job of it.
That has been the experience of Sherrill Strickland, who farms with his cousin Clay near Salemburg, N.C. The two went to automated curing controls two seasons ago.
“Before, we had used two handmade wet bulb thermometers to monitor conditions in the curing barn,” says Sherrill Strickland. “They worked fairly well, but I had to base everything on such things as visual appearance and smell.” Their control system, the MA052X-2 Automatic Tobacco Barn Temperature & Damper Control made by Cureco, is based on precise measurements of conditions inside the barn.
“The automated controls are very easy to use, very accurate and I have found them very reliable. Once we put the curing controls in, we cut curing time by one day per barn.”
There is a quality benefit also, which positively impacts yield.
“We have found we don’t have to throw away nearly as much tobacco — particularly from the first cropping — because of quality,” he says. “Don’t get me wrong — you can still mess up a barn. But what used to be a difficult problem has become an easy one.”
Before, they had controlled humidity using a manual wet bulb. “But you can’t do the job manually as it should be done,” says Sherrill. “We got by, but we were throwing a lot of tobacco away.”
“As the industry continues to consolidate, there are fewer larger growers with more interest in curing control,” says Mack Grady, president of Cureco. “They have to spread their time out in a different way as they get bigger. The most efficient farmers are the ones who are going to have a place in tobacco growing in the future.”
Automatic damper control provides continuous monitoring of the wet-bulb temperature, resulting in more accurate ventilation control and lower fuel consumption during curing, says Grant Ellington, North Carolina Extension engineer.
“The amount of fuel savings associated with any automatic damper control will depend on how well a grower is currently managing the ventilation process,” Ellington says. “Although automatic curing control systems can help to improve curing management, the desired curing conditions are inputs based on experience curing tobacco.”
Automatic control systems can also monitor the dry-bulb and wet-bulb temperatures and transmit this information electronically to a central location, such as an office or home.
“This allows the grower to observe the real-time curing conditions of each barn connected to the system,” says Ellington. “As growers continue to consolidate their barns, the remote monitoring capability has a significant time management benefit. Less time is spent opening and closing barn doors and making damper adjustments multiple times daily.”
Grady says Cureco offers a remote system for controlling curing barns. “With our system, a farmer can monitor his barns from anywhere that has internet access,” he says. “It is not as popular as the basic curing control system, but interest is growing.”
The Stricklands haven’t made the switch to remote yet. “I am too old school,” Sherrill explains.
Although the air-curing systems are not as automated as flue-cured, there is still some mechanization that a burley or air-cured farmer can apply.
For instance, a good way to determine the conditions inside the air-cured barn and inside the tobacco is to purchase commercial digital temperature and humidity instruments, says John Wilhoit, Kentucky Extension engineer. “Hang these up in the tobacco mass —but not directly against a moist leaf — to sense and record the environmental conditions.”
The conditions inside conventional air-curing barns generally follow those outside the barn, depending on air movement and the buffering action of the tobacco mass.
“The average temperature inside the barn will be slightly lower than outside because of evaporative cooling during the drying stage,” he says. “The average relative humidity inside will be higher than outside under most conditions of adequate ventilation.”
These instruments store maximum and minimum data readings. “You can view them to see the past cycle of conditions and reset as desired,” said Wilhoit. “The accuracy of relative humidity measurement is generally plus or minus 3 percent.”
In one-tier plastic-covered field-curing structures, there is normally plentiful air movement through the tobacco, said Wilhoit. You want to shield them from strong winds that can damage the plastic covering and tobacco, so place these structures downwind from fence rows or similar wooded areas that can provide protection.
“Plastic or other covering should be applied over the hanging tobacco before a significant rainfall,” he said. “It should be maintained throughout the cure for protection from rain and wind damage.”
e-mail: [email protected]
About the Author(s)
You May Also Like