July 29, 2010
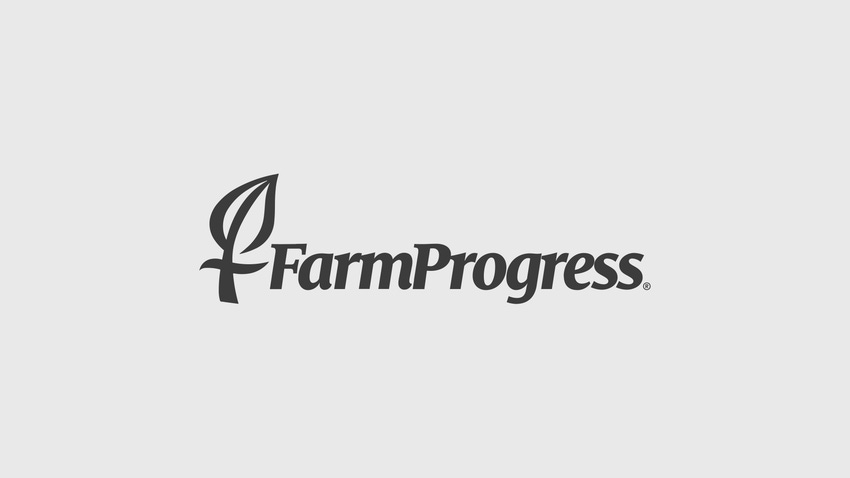
The 2009 harvest put every color of combine to the test. Wet fields. Soft cobs. Tough stalks. Higher-than-average yields. Increased amounts of material other than grain (MOG) in the field. These were the conditions that made for what some growers called the toughest harvest in 25 years.
However, going forward, are growers ever going to have a “normal” year? Here’s what they face: corn genetics capable of 300-bu./acre yields; tougher stalks and more trash to move through the combine due to Bt and other transgenic improvements; and increasing farm size. This all adds up to more grain to harvest, but no more time to do so. Toss in the additional complication of uncertain weather and growers are going to need solutions now.
So what are some of the new combine technologies that will enable growers to harvest more grain, maintain grain quality, and minimize foreign matter in the bin? We asked U.S. combine manufacturers to describe three of their newest technologies designed to tackle these mounting challenges.
CLAAS LEXION
1
Mobil-Trac System (MTS)
With half the ground pressure of most wheeled combines (average 10.5 psi), a Lexion equipped with the MTS can continue to harvest no matter the ground conditions. MTS is integrated with the combine design to reduce maintenance and allow for faster ground speeds — as high as 18 mph on the Class 9 595R model. Thirty-five-inch-wide, self-tensioning tracks with oscillating mid-rollers ensure maximum flotation and efficient tracking to improve performance and extend belt life. The MTS also offers positive traction that virtually eliminates slippage. Less slip means less impact on the soil surface and soil structure, which makes field preparation easier and less costly.
2
Claas APS hybrid system
Lexion combines use a hybrid threshing and separation system made up of a tangential (tri-cylinder) threshing system called Accelerated Pre-Separation (APS) followed by exclusive RotoPlus dual separation rotors. The operating speed of both threshing and separation can be set independently to optimize performance for maximum output and quality. The APS system pre-separates up to 30% of the easier-to-thresh crop. This crop bypasses threshing and goes directly to the cleaning system so that only the crop that needs to be threshed is threshed (aka focused threshing). This process not only increases capacity and performance but grain quality as well.
3
Grain analyzer
Optional grain analyzer sensors, located in the cleaning system just beyond the lower sieve, analyze material traveling into the returns system. These sensors allow the operator to monitor not only the amount of returns (via the volume returns sensor in the returns elevator) but also the type of material (i.e., percent grain) being returned to the APS to be re-threshed. This added information, when combined with information from loss sensors located across the entire cleaning shoe, allows the operator to adjust combine settings as conditions warrant without leaving the cab. Costly downtime can occur when the operator needs to leave the cab to adjust settings.
For more information, visit www.claasofamerica.com.
CASE IH AXIAL-FLOW
1
AFX rotor
At the heart of a Case IH Axial-Flow combine is the AFX rotor. Its impellers work with the patented transition cone to draw high volumes of tough crop material into the threshing chamber. Inside the concentric chamber are adjustable vanes to control crop flow. A recent technology development is the ST rotor, which uses a smaller diameter center tube and taller threshing and separating elements to allow higher volumes of crop material to be processed at a lower power requirement. This rotor was initially developed for the rice market and has been refined for high-capacity performance in tough, high-volume straw crops, including soybeans.
2
Cleaning systems
Case IH says it offers the industry’s largest cleaning systems for each class of combine, topping out at 10,075 sq. in. on the Axial-Flow 8120 and 9120 models. The large sieve area is combined with the patented Cross-Flow cleaning fan, which provides an even distribution and high volume of air to the sieves. The self-leveling cleaning system, standard on all 20 series models, levels the fan, grain pan, top sieve and bottom sieve on slopes up to 14%. This system enhances cleaning capacity and sample quality in a broad range of crop conditions and ground terrain, including high-yielding, high-moisture corn.
3
Corn heads
In 2009, Case IH upgraded the 3000 series corn heads by introducing longer, point-to-point stalk rolls supported by a lower bearing to more consistently process tough stalk material produced by today’s corn genetics. For more aggressive corn residue management, Case IH 2600 series chopping corn heads incorporate rotating blades beneath the stalk rolls to cut and size cornstalk residue as it passes through the row unit. Case IH 20 series combines offer three different chopper options — standard cut, fine cut and the Magna-cut — allowing producers to balance chop performance with the power requirement of the chopper, based on their crops and conditions.
For more information, visit www.caseih.com.
NEW HOLLAND CR, CX
1
IntelliCruise
The IntelliCruise Automatic Crop Feeding System automatically matches the speed of the combine to the crop load. The crop load is measured before it reaches the rotors to ensure that combine adjustments are made in anticipation of changing conditions. The instantaneous adjustment by the combine ensures that the crop load to the twin rotors is constant and maximized to allow for optimum threshing capacity and overall combine efficiency. Operator fatigue is also reduced, allowing for more acres to be harvested in a day.
2
Right-sizing
New Holland recently launched two new combine models, the CR9090 and CR9065, to “right-size” its combine lineup and increase capacity. The CR9090, with a maximum horsepower of 591, set the Guinness World Record for the most grain harvested in 8 hrs. The CR9065 is for the grower who needs more power but not a large-frame combine. It delivers a maximum 463 hp for operating in tough conditions, running a chopping corn head, unloading on the go, and running in sloped and soft terrain. New Holland claims that the combine offers the industry’s best horsepower-to-weight ratio and provides optimal capacity and efficiency.
3
Grain Cam System
This system involves a camera that recognizes the concentration of chaff and broken grain in the sample as it is transferred through the clean grain elevator to the grain tank. This information is shown on the IntelliView III monitor in the form of a graph, allowing the operator to fine-tune adjustments, further boosting grain purity.
For more information, visit www.newholland.com/na.
AGCO GLEANER R6
1
Two-auger unloading
The AGCO Gleaner uses a two-auger design unloading system to transfer the crop from the grain bin to the wagon. The system incorporates a large, 12-in. cross auger, which carries the grain to the Direct Flow unloading auger, not a sump. Eliminating the extra auger reduces horsepower requirements and wear and allows for an average unloading rate (4 bu./sec.) that is faster than that of conventional, three-auger, turret-type systems. In addition, fewer kernels are cracked in the two-auger system because the grain goes through fewer transition points.
2
Two-stage cleaning
After the crop is threshed and separated, distribution augers uniformly distribute crop to accelerator rolls, which propel grain four times faster than free fall through a high-velocity air blast onto the grain pan. This process pre-cleans the grain before the grain reaches the shoe to produce a cleaner grain sample than if the grain were cleaned by cleaning shoes alone. Because grain coming from the processor is evenly fed across the entire cleaning shoe, the combine can operate on slopes up to 23% without the need for self-leveling devices.
3
Natural flow feeding
The rotor in the Gleaner R6 series is positioned transversely instead of axially as in other rotary combines to allow for what AGCO calls “natural flow feeding.” This positioning maintains the width of the crop mat throughout the entire crop feeding process to eliminate pinch points and expand throughput capacity before the crop enters the processor. Delivered at a constant angle to the concave and cylinder, the Natural Flow system eliminates twisting and turning of the crop to constantly feed the threshing rotor, increasing performance and productivity.
For more information, visit www.agcocorp.com.
AGCO AXIAL
1
140-in. rotary
The rotor in AGCO’s axial combine platforms, including Gleaner A6, Challenger 600B, and Massey Ferguson 9005 series, is 140 in., providing high-capacity threshing and grain separation. The rotor uses six rows of rasp bars in the threshing area and three rows in the separator area, along with 21 rotor knives and an additional three rows of five separator paddles. Grain is threshed in multiple, controlled passes, then falls through the concaves in combination with centrifugal force over the separator grates.
2
Hydrostatic rotor drive
A constant-speed hydrostatic rotor draws its power from a hydraulic pump driven directly off the engine. Full-pressure hydrostatic rotor drive enables the rotor to maintain speed, even when engine rpm drops. It also provides full reversing capability.
3
Two-auger unloading
In 2009 AGCO redesigned the unloading system of its axial combines, borrowing some aspects of the two-auger design found in Gleaner transverse combines. Now all of its brands — Gleaner, Challenger, and Massey Ferguson — share a similar concept to accommodate higher yields. The unloading system incorporates a large, 12-in. cross auger, which carries the grain to the Direct Flow unloading auger. Eliminating a third auger reduces horsepower requirements and wear and allows for an average unloading rate of 4 bu./sec. In addition, fewer kernels are cracked in the two-auger, rather than a three-auger, system, because the grain goes through fewer transition points.
For more information, visit www.agcocorp.com.
JOHN DEERE STS
1
AutoTrac
A vehicle guidance system, AutoTrac steers the combine down every field pass, thereby reducing operator fatigue and ensuring an even feed of crop material into the feederhouse. Even feeding reduces overall MOG intake and machine slugging. Data from the StarFire GPS receiver are supplemented with data from mechanical feelers to guide the combine through tough conditions like down corn. The system, called AutoTrac RowSense, navigates the row units down the center of the row to help the combine maintain a constant ground speed and even crop flow, maximizing time available in the harvest window to cover more acres.
2
ProDrive
The ProDrive propulsion system uses automatic powershift transmission technology to shift between two speed ranges as ground conditions change to keep the combine harvesting at the desired ground speed. ProDrive is coupled with Harvest Smart, a feed-rate-control system, to enable automatic ground speed control during harvest. STS combines maintain a consistent crop load (feed rate) by automatically changing the combine ground speed to compensate for variations in crop that are not readily visible to the operator. This allows customers to maintain their grain quality (due to more consistent crop loads in the combine) and boost productivity.
3
4 x 4 feederhouse
The 9670 STS, 9770 STS, and 9870 STS feature a 4 x 4 feederhouse that handles platforms up to 40 ft. and weight loads up to 4,400 kg. Compared to previous feederhouse designs, this 4 x 4 structure provides the highest levels of material handling and feeding capacity, especially in high-volume, tough crop conditions. With higher yields, the 4 x 4 feederhouse allows for a smooth crop flow and faster transition of material into the combine to increase harvest productivity.
For more information, visit www.johndeere.com.
About the Author(s)
You May Also Like